100%良品を目指すと、失敗コストは下がりますが、品質コストが膨大になります。
例えば、我社は「絶対に不良品を出荷しない」とするなら、全数出荷前の検査が必要です。しかし、検査には誤差や過誤が必ずあります。良品を不良と判定する(生産者危険)もあれば、不良品に合格を出す(消費者危険)もあります。消費者危険ゼロを完全に達成するには、1つの製品も出荷できません。
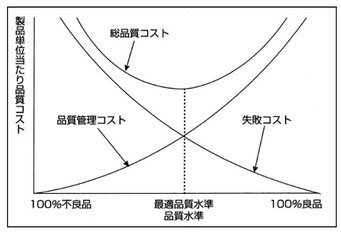
そこで、最適品質水準という考え方が出てきます。品質管理コストと失敗コストが釣り合うところまで品質水準を上げた地点、つまり総品質コストが最低となる品質水準で満足とするというわけです。
品質管理コストは自社で使っているコストですから、損益計算書を注意深く見れば計算できます。
失敗コストは、出荷前に社内で掛る内部失敗コストと出荷後に社外で掛る外部失敗コストに分けられます。内部失敗コストは、仕掛段階での修理や調整・手直し費用,在庫保管費、不良品廃棄費、設計や仕様変更に伴うコスト、などです。まぁ、難しいですが計算は可能でしょう。
問題は外部失敗コストをどう計算するのかです。不良品を出荷してた場合には、先ずはクレーム対応が必要です。お客様のところに出向き(人件費や旅費交通費がかかる)、状況を調査し、不良品を回収し、手直しあるいは代替品の納入をおこないます。とても想定し難いですが、この費用までは何とか計算できそうです。
ところが、外部失敗コストでは、今後のビジネスに与える影響を見積もる必要があります。ビジネスは信用ですから、不良品を出荷したことによて毀損した信用を補うコストを見積もるのです。信用はお金で買えないといっても、ゼロリスクではビジネスが成立しません。何らかの指標が必要です。
1つの方法としては、品質管理コストと失敗コストのそれぞれを価値毎に分解することが考えられます。品質管理コストは大きく予防コスト(労務管理・生産管理・品質管理・工程管理・設備管理など)と、評価コスト(検査・校正など)に分けるのが普通ですが、視点を変えて機能品質管理コストと安全品質管理コストに分けてみます。
機能品質管理コストは、製品がスペックを満足する機能であることを保証するコストです。これは最適品質水準の考え方がそのまま活用できます。
安全品質管理コストは、製品が購入者や使用者にとって無視できないほどのリスクは無いことを保証するコストです。こちらは、外部失敗コストが大きくなる懸念があります。最適品質水準の考え方は準用するものの、より注意が必要で、余裕度を高めに設定します。
製造業のコスト削減には品質管理コストを見直すことが重要です。
一般に、総コストの5~10%くらいが品質コストです。日本の会社では、品質優先・顧客満足度100%を掲げて、品質コストが過剰となり、収益を圧迫しているところが多いです。ときどきは、最適品質水準なのかを確認することが大事です。そのなかで、品質コストを分解して評価してみることが肝心です。