昨日の続きで、工場で使われる数学について・・
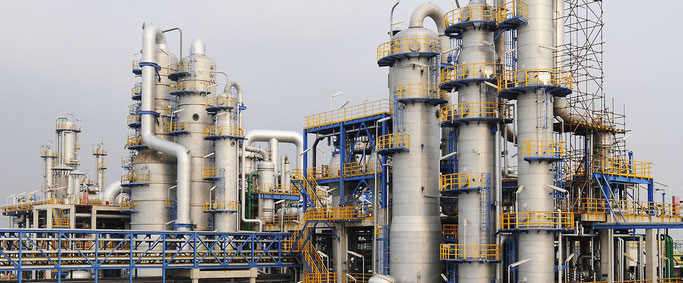
工場で勤め始めたのは32年前のことです。
当時の製造業では、QC(品質管理)とOR(オペレーションズ・リサーチ)が盛りでした。
QCは、QC七つ道具にはじまって推定・検定、実験計画法など、今にして思えば、結構高度な数学を何気に使っていました。そのなかでも、よく使われたのが「重回帰分析」です。
手順としては、先ずデータシートを作成します。~ 工程の日報から製造条件を抜き出します。途中の温度とか圧力などは、記録紙から読み取ります。検査記録などから時系列で結果を見つけます。
いろいろなテーマがありますが、このデータシートをつくるだけで1日単位の時間がかかります。
<今なら、工程のデジタルデータを吸い取るだけで数秒で済みます。>
データシートのデータをキー入力しますが、当時はオーディオカセットテープに記録していました。<これも、今なら電子メモリーに1~2秒でしょう。>
そして、このデータをもとにパソコンが計算するのですが、計算が終わるまでに数時間はかかります。<もちろん、今ならエクセルで1秒未満です。>
こうして出てきた解析結果を元にして標準製造仕様や条件変更の標準をつくります。
一度でうまく使える結果がでたらラッキーですが、半分くらいは役に立ちません。たいがいは、結果に影響を与える因子が他にもあるのに気づかずに抜かしてしまうという失敗です。
工場には本社の経理部あたりから時折「在庫削減」の指示がきます。工場としても、在庫をたくさん抱えたいというわけではないのですが、やみくもに減らせと言われても困ります。そこで、オペレーションズ・リサーチの手法を使って、科学的に最適な在庫量を示して主張します。
こういうときに、工場の製造スタッフに数学に強い人が一人いると心強いものです。
工場の品質の変化というものには、動きの癖のようなものがあります。その変化の法則性を発見できれば、変化の原因が分かって対策が打てるのですが、これが難しいのです。
工場は実験室ではないので品質に対するいろいろな攪乱が入ります。気温や風向きなど自然の環境もありますし、隣接設備の稼働状況や、ときにはオペレーターの操作方法なども影響を与えます。
そういうノイズのなかからシグナルを取り出して、それぞれの要素の相関から法則性を発見できると、工場の品質は改善されます。